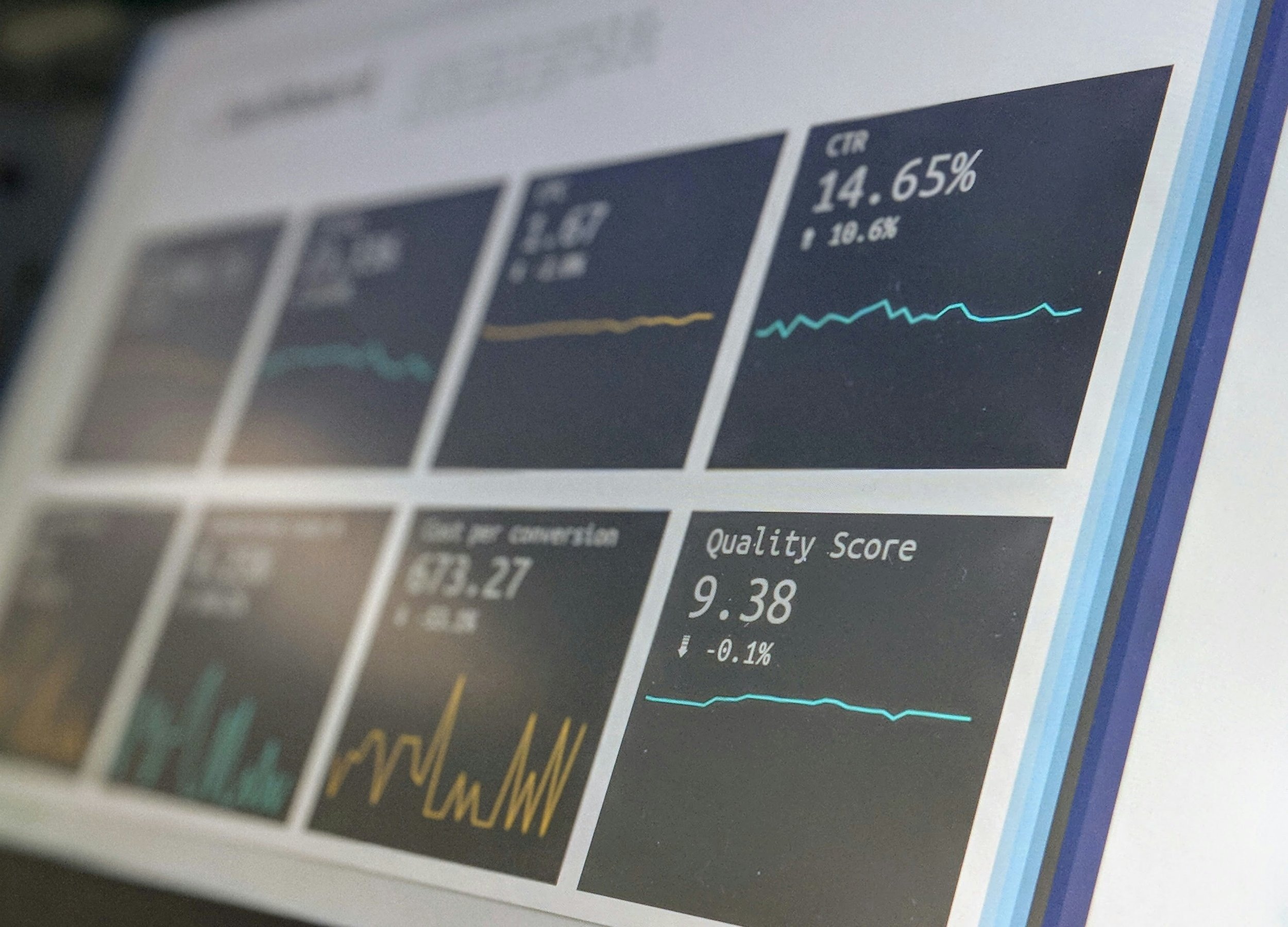
Analysis
Analysis of Tool Making Services
Tool-making services are essential for the manufacturing industry, providing the tools required for efficient production processes. This service includes designing, constructing, and maintaining molds, dies, and fixtures used in the fabrication of components. The analysis of tool-making services focuses on optimizing design and production methods to ensure precision and longevity.
Design Optimization
CAD and CAM Integration: Utilizing Computer-Aided Design (CAD) and Computer-Aided Manufacturing (CAM) software allows for precise design specifications. Engineers analyze the tool design for efficiency and effectiveness, ensuring that the geometry supports the intended manufacturing processes.
Material Selection: Choosing the right materials for tools is critical. The analysis examines material properties, such as hardness, wear resistance, and thermal stability, to ensure the tools can withstand the production environment and last longer.
Manufacturing Techniques
Precision Machining: Analyzing the methods used for tool production, such as CNC machining, ensures high accuracy. The focus is on reducing tolerances and improving surface finishes, which directly impacts the quality of the produced components.
Additive Manufacturing: In some cases, 3D printing technology is used for tool making. Analyzing the benefits of additive manufacturing, such as rapid prototyping and the ability to create complex geometries, allows for innovative tool designs that traditional methods may not achieve.
Lifecycle Management
Predictive Maintenance: An analysis of how tools perform over time is essential for planning maintenance schedules. By predicting when a tool will need maintenance or replacement, manufacturers can reduce downtime and optimize production schedules.
Tool Performance Evaluation: Regular analysis of tool performance, including wear patterns and production quality, helps identify areas for improvement. Data collected from these evaluations can inform future tool designs and manufacturing processes.
Cost Efficiency
Total Cost of Ownership: Analyzing the long-term costs associated with tool making, including initial investment, maintenance, and operational costs, enables businesses to make informed decisions about tool purchases and design.
Minimizing Scrap and Waste: Evaluating production efficiency helps identify opportunities to minimize material waste during tool making, leading to cost savings and more sustainable practices.
Analysis of Prototyping Services
Prototyping services provide a vital link between design and production, allowing manufacturers to create and test models before full-scale manufacturing. This service is crucial for validating concepts and ensuring functionality. The analysis of prototyping services focuses on the effectiveness of prototype creation and testing methods.
Rapid Prototyping Techniques
3D Printing: The analysis of various 3D printing technologies (FDM, SLA, SLS) helps determine the best method for producing prototypes based on factors like material properties, dimensional accuracy, and surface finish.
CNC Machining: Evaluating the role of CNC machining in prototype development allows for high-precision parts to be created quickly, facilitating more detailed testing.
Design Validation
Functional Testing: Prototypes are tested for real-world performance, including mechanical and thermal properties. The analysis includes assessing how the prototype behaves under stress, evaluating any potential failure points.
Iterative Feedback: Analyzing feedback from prototype testing enables rapid iterations. Manufacturers can refine designs quickly based on performance data and user feedback, improving the end product.
Material Analysis
Material Properties Evaluation: Understanding the mechanical properties of different materials used in prototyping is crucial. The analysis focuses on factors such as tensile strength, flexibility, and weight to ensure the prototype behaves as intended.
Cost vs. Performance: Analyzing the cost-effectiveness of various materials helps balance budget constraints with performance requirements, guiding material selection for both prototypes and final products.
Time-to-Market
Efficiency of Prototyping Process: Analyzing the time required to develop prototypes helps streamline the process. Identifying bottlenecks or inefficiencies allows manufacturers to accelerate development timelines, bringing products to market faster.
Analysis of Component Services
Component services encompass the design, production, testing, and ongoing support of individual parts used in larger systems. This service ensures that each component meets the specific requirements for quality, performance, and integration. The analysis of component services focuses on optimizing each part's development and lifecycle management.
Performance and Testing
Mechanical Testing: Each component undergoes rigorous testing for strength, durability, and operational performance. The analysis includes evaluating how components perform under various conditions and loads.
Quality Assurance: Implementing strict quality control measures throughout the production process ensures that components meet required specifications. Analyzing the effectiveness of these measures helps maintain high-quality standards.
Integration and Compatibility
Design Compatibility Analysis: Ensuring that components fit seamlessly into larger assemblies is crucial. The analysis focuses on tolerance levels, alignment, and integration methods to minimize assembly issues.
Failure Mode and Effects Analysis (FMEA): Evaluating potential failure modes in components helps identify risks and develop strategies to mitigate them, enhancing overall system reliability.
Lifecycle and Sustainability
Lifecycle Analysis: Understanding the lifecycle of each component, from production to disposal, enables manufacturers to implement sustainable practices and reduce environmental impact.
Repair and Maintenance Services: Analyzing the feasibility of repairing or refurbishing components can lead to cost savings and longer service life, reducing the need for new parts.
Customization and Adaptability
Tailored Solutions: Analyzing customer needs allows for the development of customized components that meet specific application requirements, enhancing client satisfaction and competitiveness in the market.
Adaptability to Changing Technologies: Keeping abreast of technological advancements enables component services to adapt quickly, ensuring that products remain relevant and high-performing.
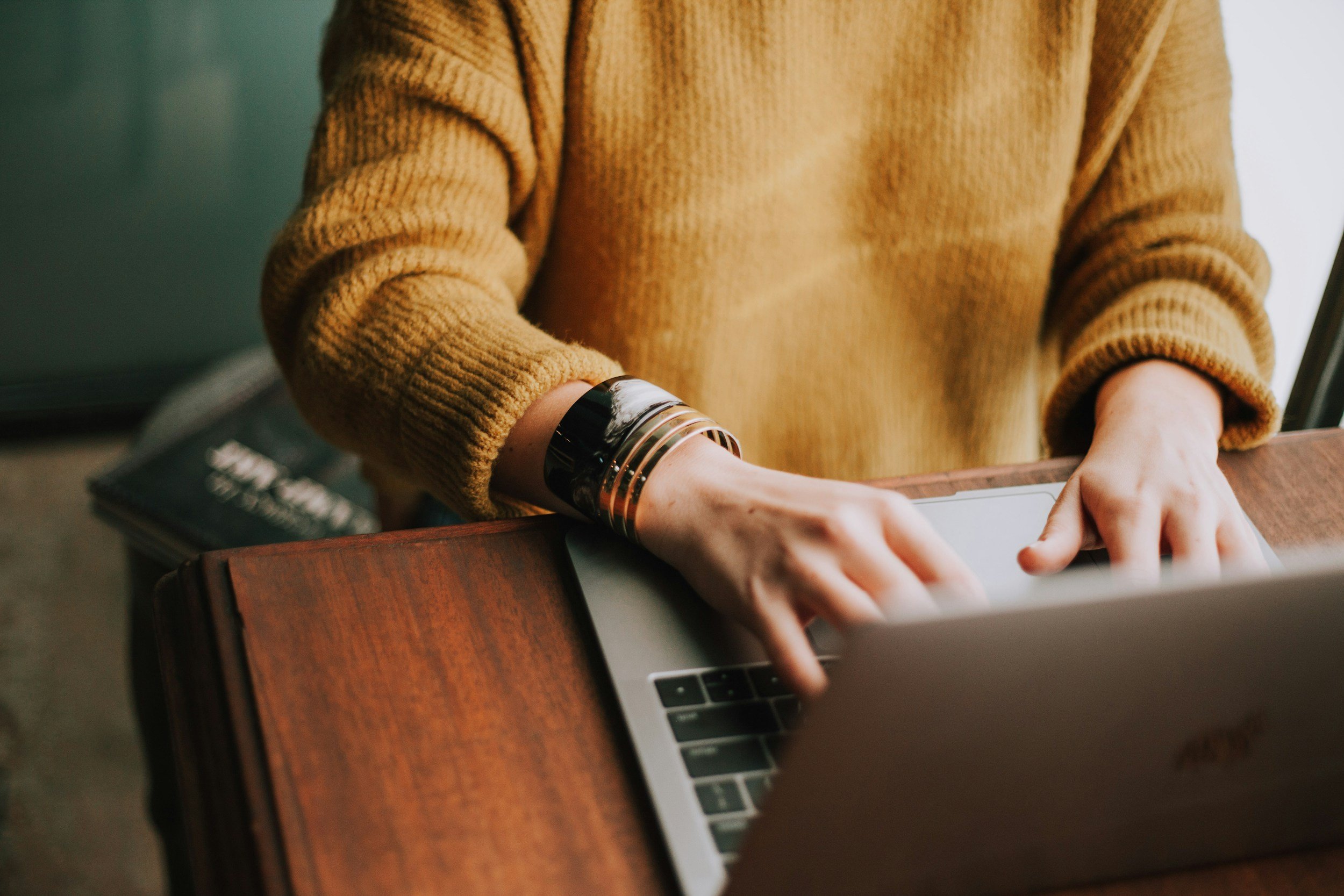